什么是TPM?
TPM的提出是建立在美国的生产维修体制的基础上,同时也吸收了英国设备综合工程学、等管理的思想。大家的TPM的理解为:利用包括操作者在内的生产维护保全活动,提高设备的全面性能。在TPM的发展历程中,共计经历了五次大的思想变革。
1、时候维修BM(Breakdown Maintenance)这是最早期的维修方式,即出了故障再修,不坏不修。
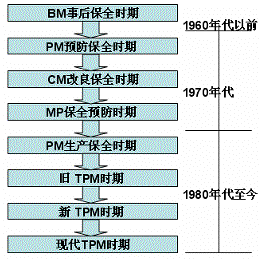
3、改善维护CM(Corrective Maintenance)改善维修时不断地利用先进的工艺方法和技术,改正设备的某些缺陷和先天不足,提高设备的先进性、可靠性及维修性,提高设备的利用率。
4、维护预防MP(Maintenance Prevention)维修预防实际就是可维修性设计,提倡在设计阶段就认真考虑设备的可靠性和维修性问题。从设计、生产上提高设备品质,从根本上防止故障和事故的发生,减少和避免维修。
5、生产维护PM(Productive Mainenance)是一种以生产为中心,为生产服务的一种维修体制。它包含以上四种维修方式的具体内容。对不重要的设备仍然实行时候维修,对重要设备则进行预防维修,同时在维修中对设备进行改善维修,设备选型或自行开发设备时注重设备的维修性。
TPM的定义
TPM的提出是建立在美国的生产维修体制的基础上,同时也吸收了英国设备综合工程学、等管理的思想。大家的TPM的理解为:利用包括操作者在内的生产维护保全活动,提高设备的全面性能。
TPM的特点
TPM的特点是三个“全”,即全效率、全系统和全员参与。
全效率:指设备寿命周期费用评价和设备综合效率。
全系统:指生产维修系统的各个方法都要包括在内。即是PM、MP、CM、BM等都要包含。
全员参加:指设备的计划、使用、维修等所有部门都要参加,尤其注重的是操作者的自主小组活动。
TPM的目的与意义
TPM的首要目的就是要事先预防、并消除设备故障所造成的七大损失:准备调整、器具调整、加速老化、检查停机、速度下降和生产不良品。做到零故障、零不良、零浪费和零灾害,在保证生产效益最大化的同时,实现费用消耗的合理化。
TPM的目标可以概括为四个“零”,即停机为零、废品为零、事故为零、速度损失为零。
停机为零:指计划外的设备停机时间为零。计划外的停机对生产造成冲击相当大,使整个生产品配发生困难,造成资源闲置等浪费。计划时间要有一个合理值,不能为了满足非计划停机为零而使计划停机时间值达到很高。
废品为零:指由设备原因造成的废品为零。“完美的质量需要完善的机器”,机器是保证产品质量的关键,而人是保证机器好坏的关键。
事故为零:指设备运行过程中事故为零。设备事故的危害非常大,影响生产不说,可能会造成人身伤害,严重的可能会“机毁人亡”。
速度损失为零:指设备速度降低造成的产量损失为零。由于设备保养不好,设备精度降低而不能按高速度使用设备,等于降低了设备性能。
推行TPM要从三大要素上下功夫,这三大要素是:
1、提高工作技能:不管是操作工,还是设备工程师,都要努力提高工作技能,没有好的工作技能,全员参与将是一句空话。
2、改进精神面貌:精神面貌好,才能形成好的团队,共同促进,共同提高。
3、改善操作环境:通过5S等活动,使操作环境良好,一方面可以提高工作兴趣及效率,另一方面可以避免一些不必要设备事故。现场整洁,物料、工具等分门别类摆放,也可使设置调整时间缩短。